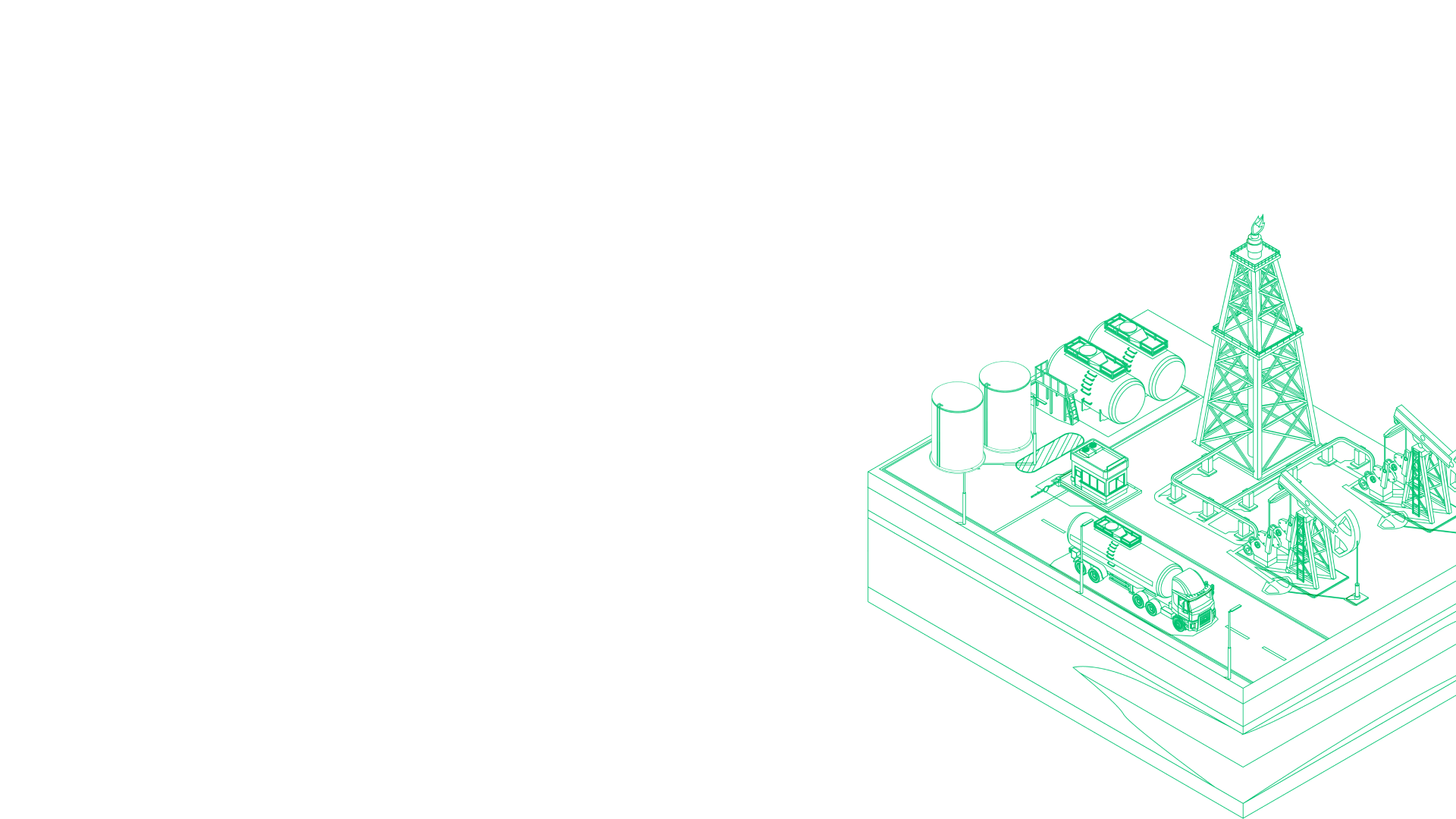
Expert Industry Insights
Get unique insights from Qube Technologies' experts to make better decisions and foster innovation.
Qube Platform Release 2.47: New Tools to Improve Emissions Management
We’re excited to announce Qube Dashboard Release 2.47, which introduces key upgrades to improve your emissions tracking and analysis. This release focuses on enhancing the user experience, streamlining data analysis, and helping you act faster when it matters most.
Qube Receives NGIF Accelerator Grant Funding to Advance Emissions Monitoring
Qube, a Global Cleantech Challenge finalist and a pioneer in environmental monitoring solutions, has developed an end-to-end continuous monitoring system that uses advanced sensors and powerful machine-learning algorithms.
Real-Time Emissions Monitoring: Operational Insights from the Field
This straightforward application of continuous monitoring technology delivers actionable operational intelligence while enhancing environmental protection efforts.
EPA Deregulation and Methane Monitoring: What Operators Need to Know
The EPA is pushing its most aggressive deregulatory effort yet, aiming to roll back key methane regulations. However, legal and procedural roadblocks could stall or block these changes, leaving operators in regulatory limbo. For now, existing EPA rules—like quarterly LDAR inspections—remain in full force. With legal battles expected to drag on for years, proactive methane monitoring is essential for compliance, asset integrity, and investor confidence. Stay ahead of the uncertainty—here’s what you need to know.
Qube’s Continuous Monitoring System Receives EPA Approval
Qube Technologies has received approval from the U.S. Environmental Protection Agency (EPA) for its continuous point-source methane monitoring system. This approval recognizes Qube’s technology as an alternative test method under the OOOO regulations, allowing operators to enhance regulatory compliance, reduce costs, and improve environmental performance through real-time emissions tracking.
Employee Spotlight: Brendan Byrne, Senior Data Scientist at Qube
Before joining Qube, Byrne spent six years at NASA's Jet Propulsion Laboratory (JPL) in Pasadena, California – four as a postdoc and two as a research scientist. This experience at one of the world's premier research institutions helped refine his expertise in greenhouse gas measurements and emissions estimation.
Congress Votes to Repeal EPA’s Waste Emission Charge (WEC) Implementing Rule
Congress has voted to repeal the EPA’s Waste Emissions Charge (WEC) rule, also known as the methane fee, which imposed financial penalties on large methane emitters in the oil and gas sector. While this eliminates the direct fee, EPA methane reporting requirements and state regulations still apply, meaning operators must continue monitoring and reporting emissions.
Employee Spotlight: Bonnie Ellwood, Customer Success Leader
Texas laid the foundation for Bonnie Ellwood's career in environmental compliance and emissions management. Her journey took a pivotal turn in 2009 when she recognized a crucial gap in the industry: the disconnect between air quality requirements and operations
Qube Dashboard Release 2.46 is Live: Enhanced Emissions Monitoring, Inspection Logging, and Improved Data Export Functionality
Qube Technologies is proud to announce Release 2.46, introducing new features that enhance emissions monitoring, streamline inspection logging, and improve data export functionality.
Employee Spotlight: Bill Tubbs, Senior Data Scientist
Qube, Bill works on cutting-edge technology in emissions detection and quantification. His current focus involves analyzing data from controlled release experiments at the CRTF, studying methane dispersion patterns, and developing advanced algorithms for emission estimation.
Methane Rules in Flux - What’s Changing & What Operators Need to Know
With the new Trump administration, methane regulations are in flux - but compliance remains essential. While some rules are being reviewed, others remain in effect, and operators need to stay prepared. Here’s a quick breakdown of what has changed (and what hasn’t) since Trump took office.
Engineered for Extremes: How Qube’s Continuous Monitoring Devices Thrive in the Harshest Conditions
Qube’s devices have been tested in some of the world’s toughest climates: extreme cold, heat, humidity, and dust. Qube has used this experience to refine our hardware to deliver reliable, durable continuous emissions monitoring anywhere in the world.
Introducing Qube Dashboard Release 2.45: Track Site Emission Status, Control Your Baselines and View Emissions Beyond Methane
Release 2.45, featuring powerful new features to help you track site-wide emissions, refine baselines, and analyze gases beyond methane. Whether your priority is emissions identification, cost savings, or regulatory compliance, these updates provide greater visibility and control over your emissions performance.
Employee Spotlight: Morgan Sauer, Logistics Coordinator at Qube
Morgan Sauer is instrumental in Qube’s success, leveraging his diverse background to bring exceptional organization to logistics and inventory management. His commitment to process optimization and adaptability ensures Qube is equipped to handle the demands of a growing business.
Don’t Let Third Parties Call Out Your Super Emitters: Stay Ahead with Qube’s Continuous Monitoring Solutions
Qube Technologies’ continuous emissions monitoring solutions provide operators with the tools to detect and respond to emissions trends before they become super emitter events. By configuring real-time alarms, operators can take corrective action immediately, preventing third-party reports and ensuring regulatory compliance.
What Sets Qube Apart? Operational Excellence in Logistics and Manufacturing
In this post, we’ll explore how our Logistics and Manufacturing Teams work in concert to deliver solutions that help your business stay ahead in the push for emissions management.
Employee Spotlight: Andrew Walsh, VP of Customer Success at Qube
From wrangling rattlesnakes to managing methane emissions, Andrew Walsh's journey to becoming Qube's VP of Customer Success is anything but conventional. Let's get to know the technical expert who's helping shape the future of emissions monitoring technology.
Meeting AER Directive 060 Updates with Qube’s Proven alt-FEMP Solutions
Qube’s continuous monitoring (CM) solutions set a new standard for emissions management. On-site sensors detect methane leaks in real time, even in adverse conditions. Advanced analytics quantify leak intensity and calculate emissions, allowing for targeted remediation planning.
Year in Review 2024: Strengthening Customer Partnerships and Accelerating Growth in Emissions Monitoring at Qube Technologies!
As the year wraps up, we’re proud to highlight the incredible progress Qube Technologies has achieved this year. Here are some highlights that showcase our growth, innovation and impact
Release 2.43 Is Live: Smarter Alarm Notifications, Enhanced Uptime Tracking, and Insightful Trends!
Release 2.43 enhances your Qube dashboard with smarter custom alarm notifications, offering personalized settings for alarm parameters and notification frequency. Admins can now monitor device uptime with 6-hour intervals and track performance across devices, sites, and organizations. Gas concentration trends are now easier to visualize with options to toggle between hourly and daily averages.